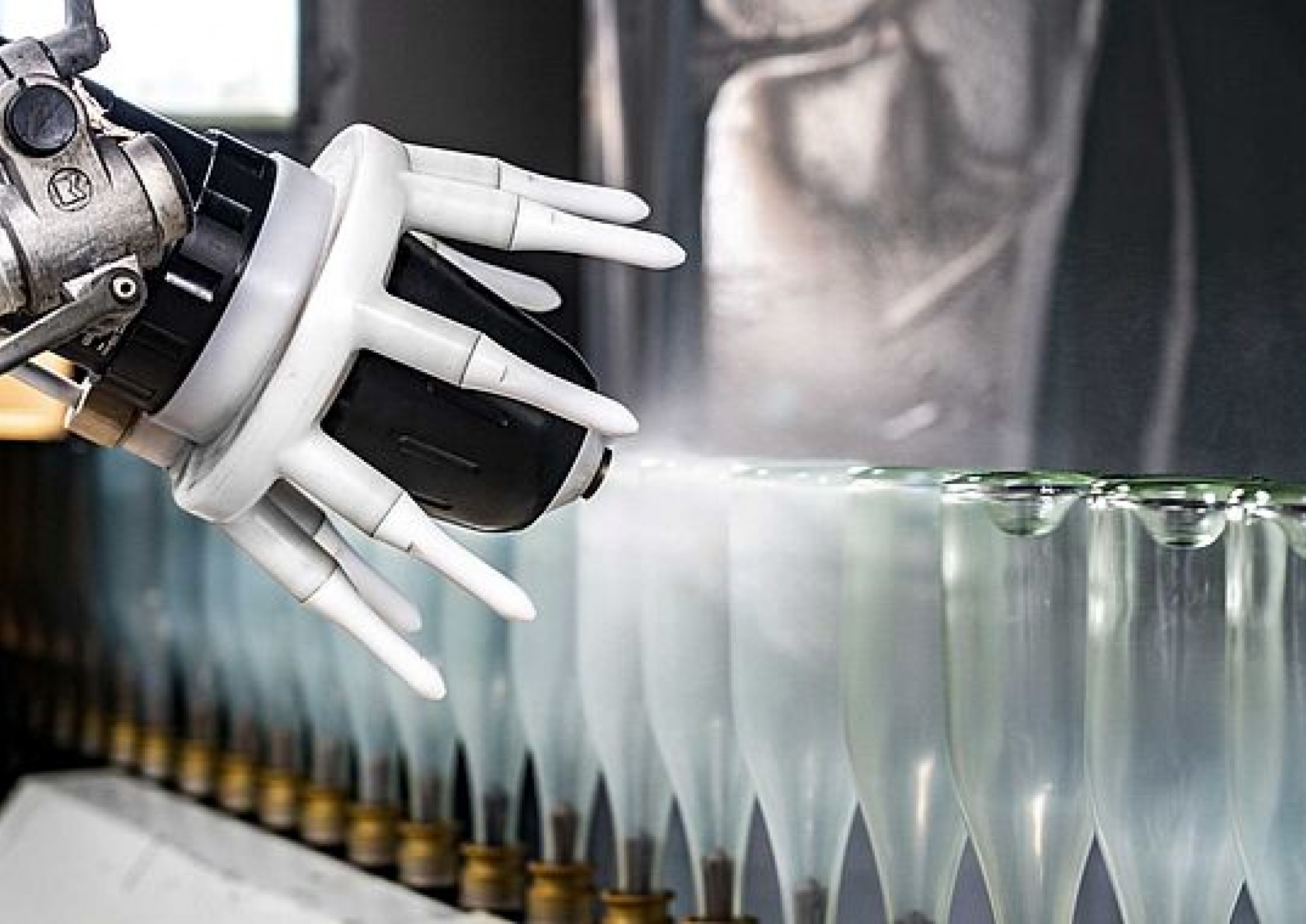
Electrostatic solution for glass bottles: How Wiegand-Glas significantly simplified its coating process
The family-run Wiegand-Glas Group manufactures and sells individual packaging concepts made of glass and PET for the beverage and food industries at several locations in Bavaria and Thuringia. The competencies of the long-established company also include services related to finishing, logistics and recycling. With almost 2,000 employees, more than 8 million glass containers are produced every day.
The challenge
At its site in Steinbach am Wald (Bavaria), Wiegand-Glas produces around 3.5 million glass containers per day. Coating plays a decisive role in the production of high-quality and resistant glass bottles with individual designs. Wiegand-Glas also attaches particular importance to a sustainable production process. In Steinbach am Wald, a system for electrostatic liquid coating had been in use for several years, which already met Wiegand-Glas' high demands in terms of material efficiency and productivity very well.
However, the previous coating process had a high level of complexity due to the processing of conductive water-based paint in combination with electrostatics. Wiegand-Glas wanted to reduce this complexity and make the entire process simpler. Due to the internal charging of the previous application equipment, the entire system was permanently under high voltage during production, and the paint supplies stood on insulated pedestals. In order to access the components during production, for example to provide a second paint container, a complex potential separation with two paint kitchens was necessary. Wiegand-Glas was therefore looking for a new, more efficient solution with optimized line lengths that would achieve the same high surface quality as the existing system. The control system was also to be more intuitive in order to minimize operating errors.
The solution
After successfully testing the WAGNER solution on site over a longer period of time, Wiegand-Glas decided to use it in the future instead of the previous solution. In order to continue to achieve the highest possible application efficiency, Wiegand-Glas also relied on electrostatics for the new liquid paint system. WAGNER supplied the application equipment, paint supply and associated control system, while the liquid coating booth of the previous system remained in place.
In a first step, the glass bottles are processed in the paint booth with the GA 1030 automatic airspray guns. The upstream guns generate an initial paint film on the glass. Due to the conductive water-based paint, the paint film forms a bridge to the ground potential. This makes the glass electrically conductive in the first place and creates an electrostatic effect. Airspray guns are also used to paint the bottom of the bottle in a different color from the main bottle.
For the subsequent electrostatic coating, the WAGNER TOPFINISH Bell 1S ECH is used, a high-speed rotation atomizer with external charging, which is mounted on a linear axis. The high voltage emitted via the electrode ring creates ambient ionization in such a way that the sprayed material is charged. This highspeed rotation atomizer was specially developed for demanding coatings with water-based paints.
Compared to the version with internal charging, the overall system does not have to be specially insulated.
The Bell 1S ECH can also be used very flexibly - the spray pattern can, for example, be adapted to suit the coating and the respective bottle shape by means of different disk sizes and adjustable steering airs. With the very fine atomization an application efficiency of over 80% can be achieved, depending on the material, the flow rate and workpiece. The liquid paint system therefore also contributes to sustainable production.
Several Zip 52 double diaphragm pumps ensure a reliable paint supply to the coating system. The system is managed by an intelligent control system that has been specially tailored to the needs of Wiegand-Glas and, among other things, allows all parameters to be stored in a recipe management system. This control concept supports users in achieving repeatable coating results in consistently high quality.
The customer experience
The major advantage of high-speed rotation atomization with external charging became apparent at Wiegand-Glas immediately after commissioning of the new system: the new concept gives application engineers permanent and safe access to the paint supply. Line lengths were optimized and changeover times between colors and paint stations were significantly reduced. The intelligent control system reduces operating errors to a minimum. In the previous system with internal charging, there was also a risk of leakage currents due to contamination on the insulated platform. Since this disadvantage is eliminated in the system with external charging, the solution from WAGNER is significantly easier to maintain and clean.
Wiegand-Glas' desire to simplify the entire coating system was fully met with the WAGNER system. With the new application equipment, very high material efficiency and excellent surface quality were achieved, which at the same time also makes the entire coating process very sustainable. Wiegand-Glas therefore considers itself very well positioned to meet the challenges of the future and to continue to offer its customers high-quality coated glass bottles, in a wide variety of shapes and sizes.
https://www.wagner-group.com/en/our-company/news/detail/electrostatic-coating-of-glass-bottles/